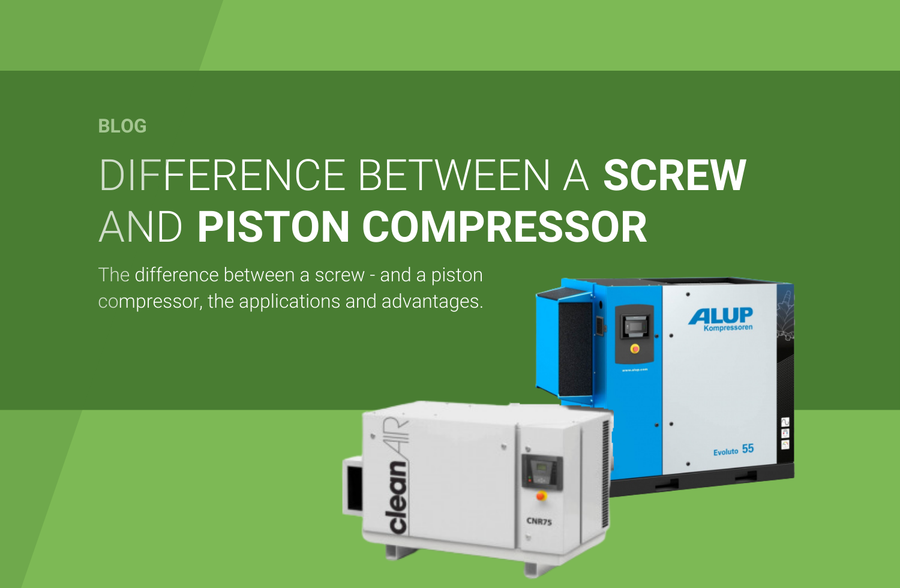
When compressing compressed air, piston compressors and screw compressors are two important options that are often considered. Each compressor has its own unique characteristics, operation, and benefits.
What are the advantages of these compressors?
Advantages of Piston Compressors
Piston compressors are suitable for applications where lower air output is needed. This makes piston compressors suitable for a wide range of applications, from pneumatic tools to production lines.
A piston compressor performs well in industrial environments and is available in both oil-lubricated and oil-free versions.
Advantages of Screw Compressors
The screw compressor is an energy-efficient solution for larger volumes and continuous 24/7 production. The rotors intermesh directly, reducing friction and energy loss compared to other techniques.
A screw compressor can operate continuously, making it ideal for applications where a constant, reliable supply of compressed air is essential.
Operation of Screw and Piston Compressors
How does a Piston Compressor work?
Piston compressors have a simple yet effective operation. The piston is driven by an electric motor and moves up and down in a closed cylinder.
When the piston moves downward, air is drawn into the cylinder through an inlet valve. The air is compressed as the piston moves back up. The compressed air is then expelled from the cylinder through an exhaust valve and stored in a pressure vessel. This process is continuous. Frictional heat generated during operation is dissipated through cooling fins. In an ideal environment, the compressor does not operate continuously to allow for heat dissipation. Piston compressors are available for pressure ranges up to 13 to 15 bar, depending on specific user needs.
A piston compressor is ideal for both small and medium applications and is known for reliability, durability, and low maintenance costs.
How does a Screw Compressor work?
Screw compressors operate with two rotating screws that intermesh—typically a male rotor and a female rotor. The male rotor has helical lobes that fit into the female rotor's grooves.
As the rotors rotate, air is trapped and pushed along the length of the rotors between the lobes. The air is compressed and moved to the end of the compressor chamber. The compressed air is then expelled through an exhaust valve. This type of compressor is often used when a constant supply of compressed air is required.
There is also a difference in drive mechanisms. The screw compressor can be driven by an electric motor through belt drive or direct gear drive.
Oil-free or Oil-lubricated Screw Compressors
There are two different types of screw compressors: oil-lubricated and oil-free, also known as dry screw compressors.
Oil-lubricated screw compressors inject oil into the compression chamber to lubricate and cool the screws. This aids in heat dissipation and sealing. Oil-lubricated screw compressors are available for large capacities. Screw compressors are also available with frequency converters. A frequency converter adjusts the compressor's speed based on consumption, resulting in significant energy savings for varying air demand.
In oil-free screw compressor technology, both rotors are driven by a synchronization gear for harmonic operation, with minimal clearance between the elements. Oil-free screw compressors have asymmetrical screw profiles, resulting in significantly improved energy efficiency.
Where are the compressors applied?
Where is a Piston Compressor applied?
Pneumatic tools powered by compressed air produced with a piston compressor include drills, impact wrenches, paint sprayers, hammers, and sanders.
In the automotive sector, piston compressors are used for pneumatic tools, tire inflation, and tasks such as collision repair or in the painting/lacquering process.
Small production lines use compressed air to operate machinery, such as in woodworking, metalworking, and the textile industry.
In medical and dental applications, piston compressors are used for medical equipment and to supply compressed air for instrumentation and surgeries.
The food and beverage industry uses both piston and screw compressors for packaging, filling, sealing, and transporting food.
Where is a Screw Compressor applied?
In industrial production, screw compressors are used for various manufacturing processes, including metalworking, manufacturing, chemical production, and glass production.
Power plants use screw compressors for operating instrument air, control systems, and various operating mechanisms.
In refineries and petrochemical plants, screw compressors are used for processes such as gas production, nitrogen generation, and gas storage.
In heavy construction and mining applications where large quantities of compressed air are needed, screw compressors are used to operate pneumatic tools, drilling rigs, and other equipment.
What is the major difference between a Screw Compressor and a Piston Compressor?
A screw compressor is typically used for higher flow rates compared to piston compressors and for 24/7 production. The screw compressor operates quieter than a piston compressor and performs better for power ratings starting from 11 to 15 kW. The choice to invest in a piston or screw compressor depends heavily on the application.
Free advice on Piston and Screw Compressor
Our specialists are happy to assist you in finding the right application and understanding the benefits of compressors for your process. For all your questions, please feel free to contact one of our specialists at info@avilo.nl or via +31(0)187 48 13 66.